Creep
of Sn-3.5Ag Flip-Chip Solder Joints in Shear
Flip-Chip Sn-3.5Ag Shear Data
Shear data for Sn3.5Ag solder joints was obtained from two
sources:
- Shear creep tests conducted by Wiese et al. (2001) on
hour-glass shaped, flip-chip solder joints of silicon-on-silicon
Sn-3.5Ag assemblies.
|
|
- Solder bumps were deposited using paste and processes
from two manufacturers. Pads were 0.1 mm x 0.1 mm or 0.2
mm x 0.2 mm and the hour-glass shaped solder joints were
0.15 mm or 0.2 mm in height. The average shear stress was
defined as the applied force divided by the narrow area
or minimum cross-section area of the hour-glass shaped solder
joints.
- Test results given in Figure 19 in Wiese et al. (2001)
were converted from shear to tensile data. The digitized
raw data is given in Table A.7 in Appendix A. The creep
tests were run at 5°C, 10°C and 50°C. Bump paste
was from two manufacturers identified by the labels DG and
PT. In Table A.7, we re-converted the tensile data to shear
using the same Von Mises transformation as was used by Wiese
et al. (equations (9) and (10) in Wiese's paper).
|
- Shear creep tests by Yang, H. et al. (1996):
|
|
- Flip-chip joints from silicon-on-silicon assemblies (33
x 33 I/O) using standard reflow were apparently barrel-shaped
with a minimum load bearing area at the joint to chip interface.
- Limited isothermal test data was available at 25°C
and 80°C. The digitized raw data, from Figure 12 in
Yang, H. et al (1997), is listed in Table A.8.
|
Comparison
of Flip-Chip and CCC Solder Joint Shear Data
|
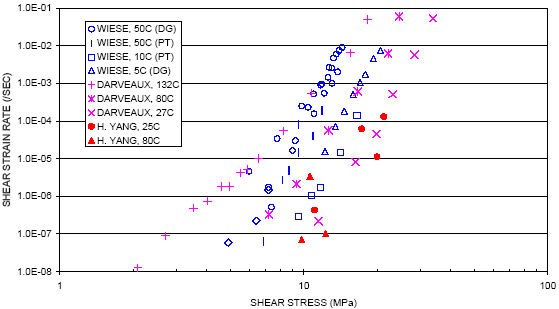 |
Figure
20: Plot of Sn3.5Ag flip-chip and CCC joint shear
creep data.
The raw shear creep data for Sn3.5Ag flip-chip and CCC solder
joints is plotted in Figure 20. Some datasets show the expected
continuity while others do not. For example:
- The 25°C flip-chip data by Yang, H. et al. shows
continuity with the 27°C CCC data by Darveaux et al.
However, the same data falls below the 10°C data points
by Wiese et al.
|
|
- Besides differences in the average stress and strain definitions,
which by themselves may lead to discrepancy in the data,
differences in the high stress locations and the solder
joint shapes may be in part responsible for the differences
between the Wiese et al. data and the other two datasets
by Yang et al. and Darveaux et al. Also, from past finite
element analysis (Lau & Pao, 1997), stress concentration
patterns are expected to be quite different for barrel-shaped
and hour-glass-shaped flip-chip solder joints. Last, differences
in the amount of terminal metals dissolved in solder may
contribute to the higher creep resistance of the Darveaux’s
CCC and Yang’s flip-chip solder joints.
|
- Of the three 80°C flip-chip data points by Yang et
al., one of them lines up with the Darveaux CCC data at
80°C but the two other data points are over one order
of magnitude below. Strangely, these two data points also
fall below the Yang’s data points at 25°C.
|
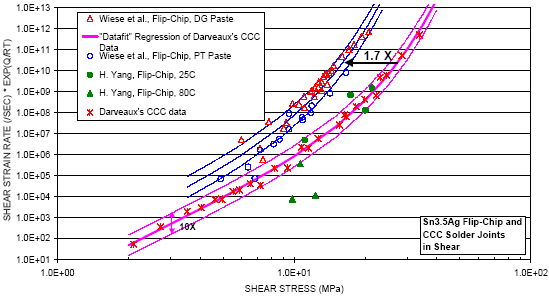 |
Figure
21: Fit of Sn3.5Ag flip-chip data to correlation
of Darveaux's CCC shear data.
The Wiese et al.'s and Yang’s flip-chip data is shown
on the plot of the Darveaux's CCC data correlation in Figure
19. The master-curve of the CCC data is as given by equation
(35) that was derived in the previous sub-section using the
"Datafit" regression of the original data by Darveaux
et al. The 10 X correlation band around the CCC data in Figure
21 is also defined by upper- and a lower-bound lines that
are an arbitrary factor 10
= 3.16 times above and below the centerline. The flip-chip
data of Wiese et al. and Yang, H. et al. is also shown on
the same plot:
- As discussed above, the 25°C flip-chip data by Yang
et al. fits rather well within or close to the CCC master
curve and correlation band.
|
|
- One of the 80°C data points from Yang et al. is close
to the correlation band (near its lower bound) whereas the
two other 80°C data points are outside and below the
band. As pointed out above, it is not clear why this is
so.
|
- The flip-chip data from Wiese et al. is outside the CCC
data correlation band and falls within a band that is offset
from the CCC master curve by a factor 1.7 X along the stress
axis. This indicates that the flip-chip data correlates
to the CCC data (within a 1.7 X factor in stress) and follow
similar trends in terms of the temperature effect. However,
the CCC joints appear to be more creep resistant and to
have higher strength. This is possibly due to more strengthening
of the CCC joints close to the soldercomponent interface,
differences in stress concentration factors for a barrel-shaped
versus an hourglass shaped joint or a combination of those
two effects.
|
|
- The Wiese et al.’s data in Figure 21 also shows
a potential "paste / manufacturing" effect. Looking
at the shifted master curve and the 10 X correlation band
around it, the majority of the "PT" paste data
points are below the centerline, whereas most of the "DG"
data points are close to or above the centerline.
|
While all of this remains to be better
understood, the above correlations of data for flip-chip and
BGA solder joints is encouraging for future reliability analysis
of solder joints of electronic assemblies. This also suggests
that, since the ultimate goal of solder testing and modeling
is to apply constitutive models to real electronic solder joints,
it is worthwhile determining solder properties from measurements
on test vehicles that closely resemble production assemblies. |