Advanced Manufacturing Processes in the Metallurgy Division
Thermodynamic and Kinetic Data
FiPy
Hydrogen Storage
Hardness Standardization
Sheet Metal Formability
Surface Roughening
Processes of Deformation
Friction during Forming
Mechanisms for Delivery of Thermodynamic and Kinetic Data
Many commercial processes are controlled by the thermodynamic and diffusion properties of the material. The ready availability of reliable data is a key component to successful design of new materials and manufacturing processes. Thermodynamic and diffusion mobility databases provide an efficient method of storing the wealth of these data, and software tools allow the user to efficiently retrieve the needed information.
NIST Contact: Ursula R. Kattner and Carelyn E. Campbell
The complexity of thermodynamics and diffusion kinetics prevented their direct application in the design of complex materials and processes in the past. Graphical representation of multicomponent systems is too complex, and, because of the enormous number, storage of every single datum is impractical. However, mathematical functions representing thermodynamic and diffusion properties of the phases permit efficient storage. Since these functions are based on physical models, they further provide the power to extrapolate binary and ternary systems to higher order systems. Software then allows calculation of the desired quantities. This approach is called the CALPHAD methodology. Unfortunately, previous software was tailored for expert users and was difficult for the occasional, less experienced user.
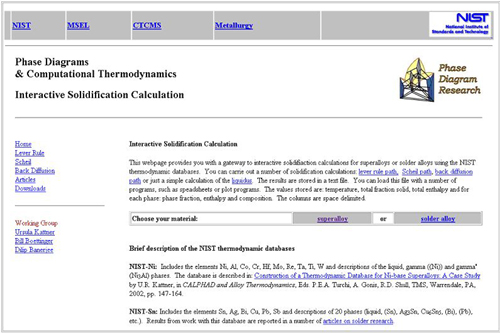
Figure 1: Web site for interactive solidification calculations.
The databases and software developed in this project are designed to provide users with simple tools to retrieve and disseminate information needed for efficient materials and process design. A web site is being developed for interactive solidification calculations using the NIST superalloy and solder thermodynamic databases (Figure 1). Results are provided in tabular form and can be used with other software packages, such as Mathematica or spreadsheets, for further manipulation. Links to a downloadable Mathematica script for DTA analysis simulation using these output tables as well as tutorial pages on the interpretation of phase equilibria information are also found on the Metallurgy Division Phase Diagram web site (www.metallurgy.nist.gov/phase/).
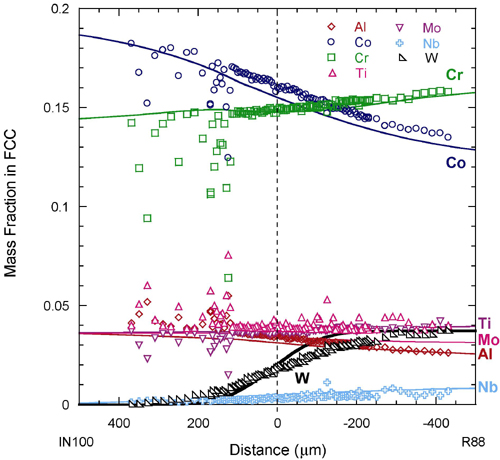
Figure 2: Experimental and calculated composition profiles for IN100/René-88 diffusion couple (1150 °C, 1000 h).
Multicomponent multiphase diffusion couples can be simulated using NIST thermodynamic and diffusion mobility databases, and experimental and calculated composition profiles can be compared. Figure 2 shows the comparison of calculated and experimental composition profiles for a γ + γ'/γ diffusion couple (IN100/René-88). The high fraction of γ' in the IN100 alloy leads to the observed experimental scatter on the left-hand side. Efforts to incorporate the diffusion in ordered phases such as B2 (NiAl) and γ' (Ni3Al) are being pursued. Future work will assess the diffusion mobilities in the Ni-Al-Cr system for the B2 and γ' phases.
Interactions developed through our "High Throughput Analysis of Multicomponent Multiphase Diffusion" workshop series are posted at (www.ctcms.nist.gov). The NIST Diffusion Data Center is being converted into an electronic searchable form, and a preliminary version is now available at .
Contributors and Collaborators
W.J. Boettinger (Metallurgy Division, NIST); A.R. Roosen (CTCMS, NIST); J.-C. Zhao (General Electric)
Back to Top
FiPy: An Adaptable Framework for Phase Field and Level Set Modeling
Phase field and level set methods have enjoyed considerable success for phase transformation modeling. However, any but the simplest implementations of these methods are beyond the capabilities of otherwise interested researchers. An adaptable software tool is being developed to support these scientists.
NIST Contact: Jonathan E. Guyer and Daniel Wheeler
The equations that model the evolution of many physical, chemical, and biological systems have a remarkably similar form. Despite the common mathematical structure of these models and the common approaches to solving them, most research codes are developed by individuals for one particular problem and then abandoned. They tend not to be documented well enough nor designed well enough to be adapted by other scientists. In fact, many scientists have difficulty adapting their own previous codes and opt, instead, to start from scratch for each new problem.
Another problem with research codes is that they are often implemented with the solution schemes that result in a functioning code in the shortest amount of time. As a result, little advantage is taken of sophisticated numerical techniques that could allow dramatically faster solutions, over larger physical domains, for longer elapsed simulation times.
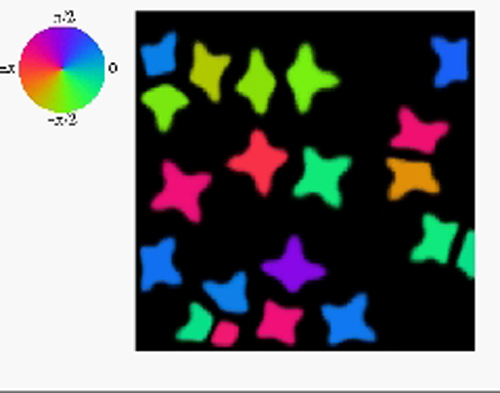
Figure 1: Phase field calculations of anisotropic grain growth.
A software framework called FiPy has been jointly developed in the Metallurgy Division and the Center for Theoretical and Computational Materials Science (CTCMS) to address this constant reinvention of phase transformation codes. FiPy is based on the finite volume method of solving PDEs, which is widely employed inthe demanding field of computational fluid dynamics. The goal of the project has been to encapsulate existing libraries and tools for tasks such as sparse matrix solutions and data visualization into a framework that is approachable by materials scientists. At the same time, every aspect of the tool is open, allowing anyuser to adapt, extend, or improve as they desire.
First released in November 2004, FiPy is already being used for phase field work by researchers at NIST andelsewhere. Existing codes have been re-implemented in FiPy, making them easier to understand and opening them to a wider battery of solution methods. FiPy has also enabled prototyping new problems in a matter of hours, rather than the days or weeks that were previously required. In addition, FiPy is being applied to new models of both cell chemotaxis and drug delivery.
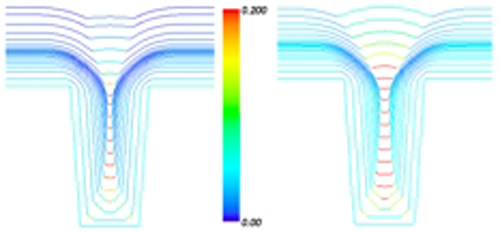
Figure 2: Level set calculations of "superfill."
Perhaps the greatest success of the tool has been to allow dissemination of NIST's Curvature Enhanced Accelerator Coverage (CEAC) model to researchers outside of NIST. This model of electrochemical "superfill" has successfully explained many aspects of the metallization of microchips, however the FORTRAN-based level set code to implement the model was impractical to use by anyone other than its author. Since being re-implemented in FiPy, the code has already been put into use by both industrial and academic researchers. The FiPy implementation of CEAC was highlighted by John Dukovic of Applied Materials in his Electrochemical Research Award Address at the 2004 Electrochemical Society meeting. FiPy can be obtained via the web at http://www.ctcms.nist.gov/fipy.
Contributors and Collaborators
J. Warren (Metallurgy Division and CTCMS, NIST); D. Saylor (FDA); W. Losert (University of Maryland); J. Dukovik (Applied Materials); Y. Shacham-Diamand (Tel-Aviv University and Waseda University); D. Lewis (General Electric)
Back to Top
Metrology Tools to Accelerate Industrial Development of Solid State Hydrogen Storage Materials
Realization of the "Hydrogen Economy" will require technological advances in hydrogen production, storage, and fuel cell implementation. Hydrogen storage poses the greatest technical challenge, and solid-state storage of hydrogen in metal hydrides will eventually be required to alleviate the safety issues associated with on-board vehicular storage of high pressure or liquefied hydrogen. The current state of metal hydride storage technology falls far short of targets for vehicular applications. A suite of versatile measurement tools is needed to accelerate the development of hydrogen storage materials.
NIST Contact: Leonid A. Bendersky, Ursula R. Kattner, and Martin L. Green
The hydrogen economy has enormous potential to make the United States less dependent on foreign sources of energy, as well as create a healthier global environment. In 2003, the hydrogen-powered "Freedom Car" was put forth as a grand challenge to the American people, and funded at the level of $1.2B. Of the three enabling technologies necessary for the realization of this vehicle, i.e., hydrogen production, storage, and fuel cell implementation, hydrogen storage is viewed as the biggest obstacle.
On-board storage of high-pressure or liquefied hydrogen, the most direct approach, has insurmountable safety issues. In addition, neither liquid hydrogen (8.4 MJ/L) nor high-pressure (133 MPa) hydrogen(4.4 MJ/L) meet the fuel energy density specificationof 10 MJ/L established for the Freedom Car. Solid-state storage of hydrogen in metal hydrides is a safer alternative for automobiles, as well as for ships, aircraft and spacecraft. However, the development of solid-state hydrogen storage materials poses many challenges, and current materials fall far short of the Freedom Car goals.
Major limitations of metal hydride storage are as follows: energy density is presently limited to about 4 MJ/L; desorption behavior (delivery) is not sufficiently rapid; excessive heat is evolved as a result of hydrogen adsorption ("filling up"); the fundamental thermochemistry of hydrides and hydrogen adsorption and desorption kinetics are a poorly understood function of composition and microstructure; finally, reliability of the hydrides, i.e., fatigue and degradation during reversible hydrogen cycling, is not known.
The goal of this project is the development of new high-throughput measurement methods to study this extremely important phase transformation in a wide variety of metal and intermetallic-based hydrides, thereby providing tools for industry to develop these materials at a greatly accelerated pace.
A multidisciplinary approach is used to address some of the major problems associated with solid-state hydrogen storage: (i) development of IR emission spectroscopy and microcalorimetry-based high-throughput metrologies for measuring hydrogen adsorption and desorption kinetics, as well as thermochemical parameters of metal hydrides; and
(ii) development of thermodynamic and kinetic dataunderlying this behavior, to guide future development.
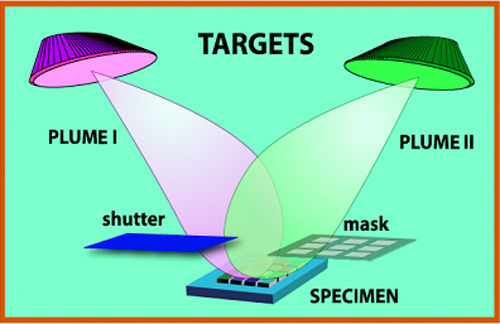
Figure 1: Synthesis of combinatorial continuous compositional spreads.
During the initial phase of this project, combinatorial film libraries of a metal alloy system have been fabricated in a form of thin film continuous compositional spreads. Initial systems include: Fe2Ti-FeTi2, Ni-Mg, and Zr35Ni65-xVx. The synthesis of the compositional spread is verified by EDS, x-ray diffraction, and cross-sectional TEM. The construction of the reaction chamber for the hydrogenation and IR measurement experiments has been initiated. Special precautions were made in the design to address safety issues arising from working with hydrogen gas at elevated temperatures and pressures.
For the construction of the thermodynamic database, the available Gibbs energy functions of the alloy systems and the metal hydride are also being evaluated.
Contributors and Collaborators
D. Josell (Metallurgy Division, NIST); L.P. Cook (Ceramics Division, NIST); E.J. Heilweil (Physics Lab, NIST); S. Semancik (CSTL, NIST)
Back to Top
Hardness Standardization: Rockwell, Vickers, Knoop
Hardness is the primary test measurement used to determine and specify the mechanical properties of metal products. The Metallurgy Division is engaged in all levels of standards activities to assist U.S. industry in making hardness measurements compatible with other countries around the world. These activities include the standardization of the national hardness scales, development of primary reference transfer standards, leadership in national and international standards writing organizations, and interactions and comparisons with U.S. laboratories and the National Metrology Institutes of other countries.
NIST Contact: Carlos Beauchamp and Sam Low
At the international level, the Metallurgy Division is leading the Working Group on Hardness (WGH) under the International Committee for Weights and Measures (CIPM), with a goal to standardize hardness measurements worldwide. As Secretary of the WGH, we have led an effort this year to better define the Rockwell hardness test procedure used by National Metrology Institutes (NMIs). The new definition is awaiting approval by the CIPM. Other activities include chairing the ASTM-International Committee on Indentation Hardness Testing and heading the
U.S. delegation to the ISO Committee on HardnessTesting of Metals, which oversees the development of the organizations' respective hardness programs.
In conjunction with ASTM International and IMEKO, the Metallurgy Division organized the HARDMEKO 2004 Conference, an international conference for scientists and specialists involved in the measurement of hardness (see Figure 1). The conference was very successful, bringing together an international audience to hear over 25 technical presentations by experts from 11 countries.
Our primary task at the national level is to standardize the U.S. national hardness scales and to provide a means of transferring these scale values to industry. Currently, we are producing test block Standard Reference Materials® (SRMs) for the Rockwell, Vickers, and Knoop hardness scales, as well as developing new reference standards. A new microindentation standardizing machine has been acquired and is currently undergoing testing and uncertainty analysis. Vickers and Knoop microindentation SRMs are available at hardness levels of 125, 600, and 760 kgf/mm2. Additional hardness levels are being investigated ranging from 900 to 1,400 kgf/mm2. These blocks will significantly extend the range of microindentation SRMs offered by NIST.
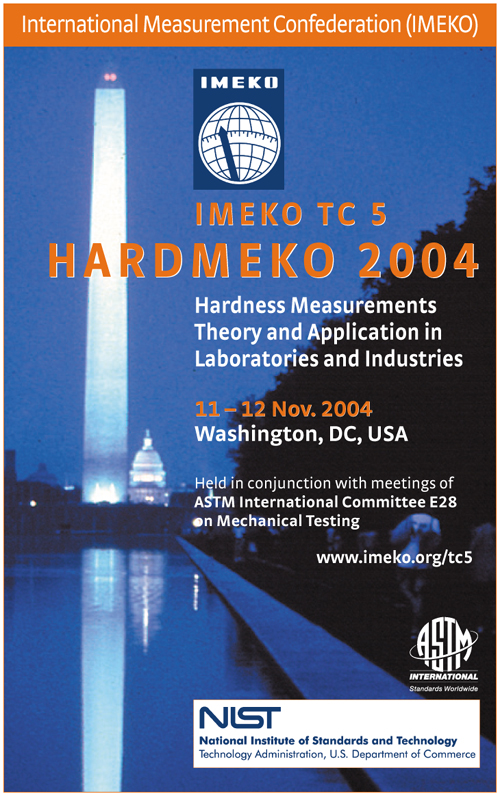
Figure 1: HARDMEKO 2004 Conference organized by NIST with ASTM and IMEKO.
In addition to newly introduced Standard Reference Materials® (SRMs) for the Rockwell B scale and three SRM Rockwell C scale blocks currently available, we are in the process of producing new SRMs for the HR15 N and HR30 N Rockwell scales. The N scales are used primarily for measuring thinner gage material or case depth. Work is also continuing to produce a new Rockwell hardness diamond indenter SRM. A joint project with Gilmore Diamond Tools has recently demonstrated that diamond indenters can be repeatedly produced with the correct shape and adhere to the very tight calibration grade tolerances.
Other activities at the national level occurring this year included the assessment of commercial secondary hardness calibration laboratories for the NIST National Voluntary Laboratory Accreditation Program (NVLAP) and the development of indentation Finite Element Analysis models used to analyze effects of different indenter materials for all Rockwell hardness scales in support of proposed revisions to international test standards.
Contributors and Collaborators
J. Fink, D. Kelley, L. Ma, H. Gates (Metallurgy Division, NIST); J. Song (MEL, NIST); W. Liggett, Jr., N. Zhang (ITL, NIST); S. Doty, B. Belzer, D. Faison (NVLAP, NIST); W. Stiefel (TS, NIST); M. Mihalec (Gilmore Diamond Tools, Providence, RI)
Back to Top
Standard Tests and Data for Sheet Metal Formability
In order to meet goals for fuel efficiency, the U.S. automotive industry is moving to lighter, high-strength materials for auto bodies. NIST has surveyed the industry and found that accurate material properties and methods for die designers to incorporate them into finite element models of sheet-metal forming dies, is a critical need for the U.S. auto industry. This project seeks to develop new standard tests and metrology to accurately determine sheet metal mechanical response under forming conditions.
NIST Contact: Timothy J. Foecke and Mark Iadicola
Successful introduction of new high-performance alloys into automotive production requires comprehensive data on alloy behavior under realistic forming conditions. Existing tests are inadequate. This project is developing two sheet metal formability tests, along with associated metrology, that can be standardized and used by industry.
Work on the first formability test, the springback cup, was undertaken at the direct request of industrial representatives in the United States Council for Automotive Research (USCAR). Springback is the shape change that occurs during elastic relaxation of the residual stresses that develop during the stamping process. Accurate springback predictions would greatly decrease the cost and number of iterations required for producing stamping dies.
The proposed test for springback consists of splitting open a ring cut from the sidewall of a deep drawn cup. The springback cup test was submitted to ASTM, and a subgroup has been formed to seek its standardization. In addition, an alternative springback standard based on stretch flanging over a cylindrical mandrel, developed by Kuwabara of Japan, has been submitted to ISO, with NIST staff developing the ASTM commentary on shortcomings of the standard geometry and procedures.
The second test method under development uses unique X-ray system that allows the direct, in situ measurement of stress in a given direction while the sample is under multiaxial load. This year we have made significant progress in mapping the multiaxial stress-strain surface for DQSK steel, an industry workhorse alloy, as well as high-strength steels such as HSLA and DP600. As with the aluminum alloys studied last year, both the flow stress and the hardening exponent were found to differ in the transverse and rolling directions of the sheet. These data will be used by industry to eliminate several assumptions that extrapolate estimated biaxial flow behavior based on a series of uniaxial tensile tests. This should lead to more accurate designs and cost savings.
This year, NIST was asked to generate materials property data for simulations of prototype parts as part of the NUMISHEET 2005 conference. In addition, the NUMISHEET 2005 benchmark tests are adding a new level of complexity by requiring modelers to predict stresses at specific sample positions during a benchmark forming process. NIST provided the corresponding measurements using our unique capabilities described above. This work also will be the subject of a plenary presentation at NUMISHEET 2005.
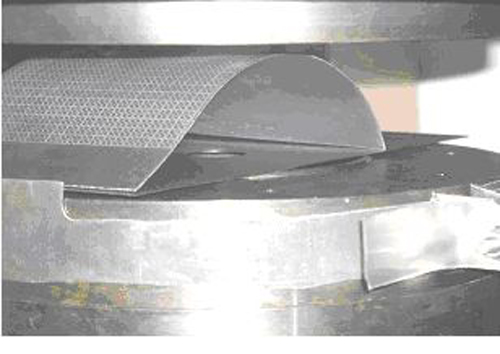
Figure 1: NUMISHEET benchmark sample loaded for plane strain deformation.
Plans for the upcoming year involve completing measurement of the multiaxial stress–strain surfaces for several alloys. This project will determine how the flow surface evolves with different types and amounts of multiaxial prestrain in a collaboration with modelers at GM. In addition, studies to date show that the influence of plastic strain on the elastic modulus of the material appears to be significant, and we intend to quantify the affect of plastic strain state and magnitude on the effective x-ray elastic constants of aluminum and alloy steel sheet.
Contributors and Collaborators
R.F. Fields; T. Gnaupel–Herold (NIST Center for Neutron Research); M. Shi (USS); E. Chu (ALCOA); C. Xia (Ford); T. Stoughton, M. Wenner, C.T. Wang (GM); J. Siekirk (DaimlerChrysler)
Back to Top
Microstructural Origins of Surface Roughening and Strain Localizations
Existing data, measurements methods, and basic understanding of metallurgical factors that influence friction, tearing, and surface finish during sheet metal fabrication are insufficient to meet the predictive modeling requirements of the automotive industry. This project addresses the measurement and data needs through evaluation of the microstructural origins of the distribution of slip, surface roughening, and strain localization during plastic straining. These studies focus on the relationships between initial material characteristics and deformation behavior of aluminum and iron base sheet. New protocols have resulted that incorporate high-resolution confocal microscopy imaging to assess the roughening character over an entire field of view.
NIST Contact: Mark R. Stoudt and Stephen W. Banovic
Lightweight materials, such as high-strength steels and aluminum alloys, are designed to reduce vehicle weight and increase fuel economy. The widespread use of these new alloys in automotive components is limited, however, by insufficient property data and constitutive laws required for accurate numeric predictions of the mechanical behavior and friction during metal forming processes. One approach to meeting these critical data needs is a careful examination of the structure property relationships that directly influence formability.
The inability to reliably predict the deformed surface morphology with numeric methods raises serious questionsas to how well the analytical tools employed to interpret roughness data actually represent the real surface. The underlying principles used to interpret surface roughness measurements were examined to ascertain the magnitude and source of any inconsistencies. The study assessed the variability within the surface roughness data that occurs over a surface by acquiring multiple roughness profiles from regularly spaced locations on an image (Figure 1) and establishing the actual form of the data with a set of mathematically rigorous protocols.
Most roughness analyses tacitly assume that a measured profile is completely described by ideal Gaussian statistics. However, the deviations observed in the skew and kurtosis data in this study revealed that roughness profiles taken from plastically deformed surfaces do not exhibit an ideal Gaussian form. The significance of this conclusion is twofold: first, non-Gaussian behavior means the roughness is produced by a small number of active mechanisms. This agrees with the literature in that deformation-induced surface roughness is primarily crystallographic slip and near grain boundary deformation. Second, these deviations from ideal Gaussian behavior provide direct evidence that the roughening behavior of a polycrystalline material can not be accurately characterized with any parameter that presumes an ideal Gaussian form(i.e., mean(Ra) or rms(Rq)). These parameters also compress the complex surface information within a profile into a singular expression that can be quite coarse with respect to the length scale of the surface features.
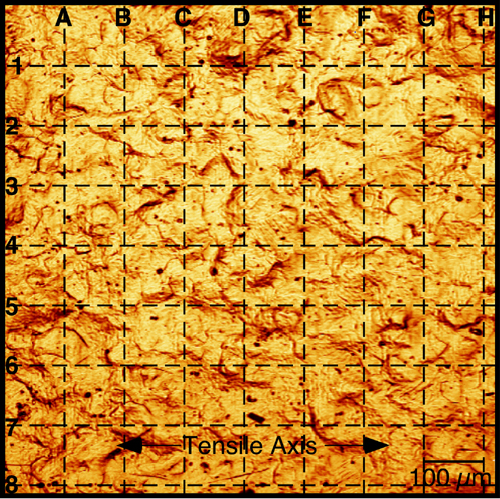
Figure 1: Scanning laser confocal image of the surface produced by 12 % uniaxial strain in AA6022. The dashed lines indicate the general locations where surface roughness data were acquired.
Since surface roughness evaluations are highly dependent upon the statistical methods used in the analysis, small deviations from the ideal condition, such as those produced by plastic deformation, are likely to have pronounced influences on the accuracy of the analytical methods used to interpret the roughness data. Hence, the current practice of extrapolating averaged, compressed values into representations of an entire surface in a particular strain condition introduces substantial measurement error into numeric predictions of behavior. Expressions are being developed to more accurately represent the stochastic nature of variations in surface roughness.
Contributors and Collaborators
J.B. Hubbard, R.E. Ricker, L.E. Levine (Metallurgy Division, NIST); S.A. Janet (ITL, NIST); R. Reno, E. Moore (UMBC); J.T. Liu (ALCOA)
Back to Top
Underlying Processes of Plastic Deformation in Metal Alloys
A substantial increase in the use of aluminum alloys and high-strength steels in automobiles would greatly increase fuel efficiency. The primary reason why this has not yet occurred is a lack of accurate deformation models for use in designing the stamping dies. This project is developing a physics-based model of plastic deformation using a combination of statistical physics approaches, atomistic modeling, and advanced measurement techniques.
NIST Contact: Lyle E. Levine
Plastic deformation of metals (as in cold rolling, stamping, drawing, and metal fatigue) is a topic of great importance to industries worldwide, and improvements in the basic technology would have a significant impact on our economy. Unfortunately, existing constitutive equations cannot accurately predict the material behavior, and many tryout and redesign steps are required. Another related difficulty is in the design of new alloys with improved formability characteristics. Currently, alloy design is done empirically with little understanding of how the various constituents affect the mechanical properties.
In the current work, we have developed a theoretical framework called the segment length distribution (SLD) model for fcc single crystals that describes how macroscopic deformation arises from the statistical behavior of large numbers of dislocations. Although work on the SLD model is continuing, the primary emphasis over the past year has been on validation testing with Washington State University and new experimental measurements of the distribution of stresses within dislocation cells (with the University of Southern California and Oak Ridge National Laboratory). These stresses could affect the assumptions used in the SLD model.
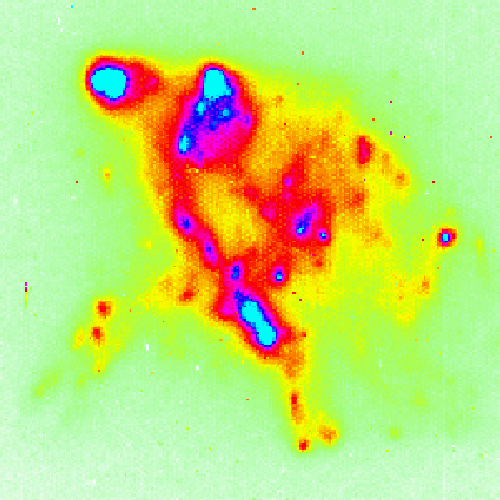
Figure 1: PSE data from Al single crystals.
Single crystal aluminum tensile specimens are being produced at NIST for the validation tests. These specimens are then strained, in situ, in ultra-high vacuum. A pulsed ultra-violet laser produces photostimulated electron (PSE) emission from fresh (unoxidized) Al in the slip lines/bands, and the electrons are collected by an electron multiplier. These time-resolved studies allow us to measure the time dependence of slip line/band production and compare these results to SLD model predictions. The SLD model predicts intermittent slip events under some conditions. Figure 1 shows preliminary PSE results that are consistent with these predictions.
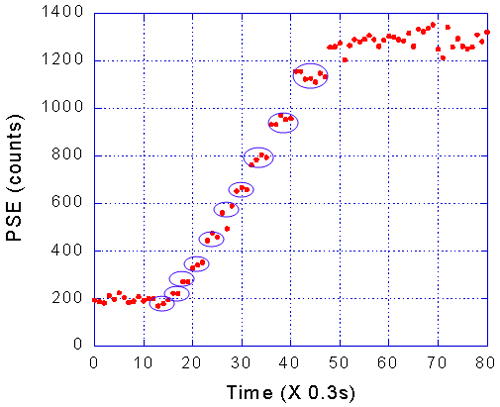
Figure 2: 117 reflection from deformed Cu crystal.
Preliminary measurements of residual stresses inplastically deformed Cu single crystals were carriedout using X-ray micro-beams at the Advanced Photon Source, Argonne National Laboratory. Spatial resolution(in all three dimensions) is approximately 0.5 µm. Large fluctuations in elastic strain (and thus stress) were observed over length scales consistent withdislocation cells. Figure 2 shows an integrated energyscan of a 117 reflection from a Cu single crystal deformed 24 % in compression. The localized and diffuse features originate primarily from dislocationcells and cell walls, respectively.
Finally, NIST researchers served on the executive committee of Dislocations 2004, and were co-organizersof Fall 2004 MRS and Plasticity 2005 symposia.
Contributors and Collaborators
F. Tavazza (Metallurgy Division, NIST); A. Chaka (Physical and Chemical Properties Division); T. Dickinson, S. Langford, M. Cai (Washington State University); M. Delos-Reyes, Z. Gao, M. Kassner (University of Southern California); B. Larson, W. Yang (Oak Ridge National Laboratory)
Back to Top
Evaluation of Friction Behavior During Metal Forming
Unpredictable friction resulting from inhomogeneous surface deformation is a significant obstacle to the widespread introduction of new high-strength alloys in the automotive industry. Metal-forming computer models still rely heavily on empirical friction data. Most existing approaches are unable to address the strong influences that variations in metallurgical condition have on the dynamic material properties and on the evolution of surface roughness. This project addresses the need for improved friction measurements, data, and models, which will allow the auto industry to improve die design and processes for forming lightweight, high-strength sheet metal alloys.
NIST Contact: Mark R. Stoudt
Many new alloys intended to decrease automobile weight are sensitive to variations in processing conditions. This variability causes inconsistencies in predicted friction behavior that exacerbate the forming difficulties. Traditional measurements normally focus on friction mechanics and do not account for the strong influences that dynamic loading and variations in metallurgical conditions have on the material properties. Hence, the friction values selected for a finite element analysis (FEA) simulation may not fully reflect the actual metal behavior under those particular conditions. Since one measurement cannot provide all essential data, new approaches are needed that: (a) evaluate both static and dynamic properties, and (b) improve the understanding of the relationships between friction and microstructural variations that affect properties during metal forming.
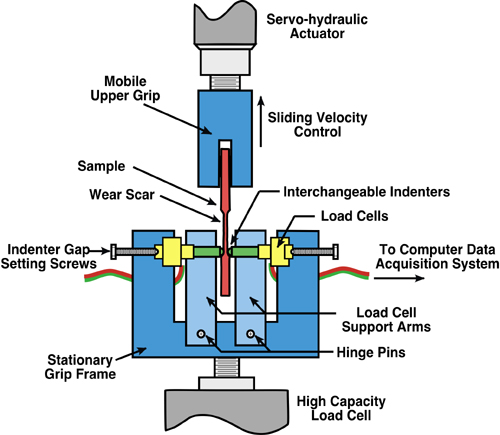
Figure 1: Schematic diagram of the prototype friction apparatus.
A single-pull measurement protocol (shown schematically in Figure 1) that produces friction data under a wide range of carefully controlled loading and strain conditions to help meet this critical need is under development. The principal advantage of this technique is that it enables direct assessment of the influences of metallurgical variables (i.e., grain size, orientation effects, strengthening mechanisms, slip homogeneity) as well as microstructural changes that are produced during deformation. This new information is anticipated to guide the development of improved numeric models that predict the final shape of formed parts.
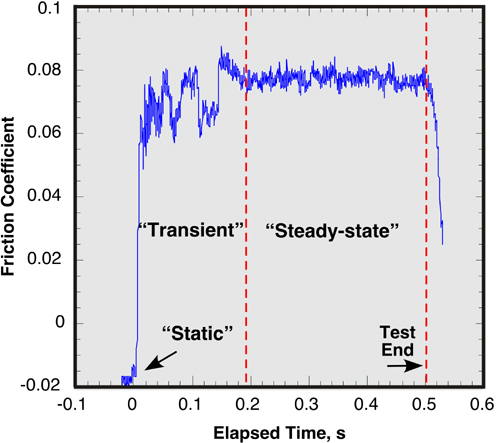
Figure 2: Variation in friction coefficient as a function of time for lubricated DQSK steel under a 1250 N indentation force.
The suitability of this approach was established through a series of friction experiments conducted on hot-dipped draw quality semi-killed (DQSK) steel. The data in Figure 2 demonstrate that the prototype can easily distinguish the transition from the static tothe sliding state and that the magnitude of the friction coefficient can be determined in real time at any point during the test. In addition, the measurement sensitivity of the apparatus is such that the quality of the resulting data is amenable to detailed statistical analysis.
Results to date indicate that the measurement protocol is appropriate for further development. A matrix of experiments is planned to further evaluate the influences of initial surface roughness and asperity distribution, strain rates and surface lubricants.
Contributors and Collaborators
S.P. Mates, J.B. Hubbard, D.J. Pitchure, R.E. Ricker, L.E. Levine (Metallurgy Division, NIST); G.B. Dalton, (TribSys, Inc.); D.E. Green (University of Windsor)
Back to Top
|